Target Tracking System X-Rz-Ry | Calibration and training platform for optical target tracking systems
Precision Assemblies and Components
782464:002.26
The X-Rz-Ry system has been specifically developed for the calibration and real-time training of EO/IR sensors, gimbal platforms, and mirror tracking systems. It combines high dynamics, precise motion control, and flexible configurability in a compact mechanical structure – optimized for use in test benches, hardware-in-the-loop environments, and validation of tracking algorithms.
The system features three active degrees of freedom:
- X-axis (translation): 500 mm travel
→ Speed up to 1500 mm/s, acceleration up to 1.5 G
- Rz (rotation around the vertical axis): ±160°
- Ry (rotation around the horizontal axis): ±6°
|
|
|
|
Options:
|
Reliable and robust standard technology
X-axis translation is powered by an iron-core linear motor from the PLT series using 600-volt technology, designed for extreme dynamics and precise trajectory control. The rotational axes are based on an adapted rotary stage (DT310) and a high-resolution linear unit coupled via a flexible rod joint. This mechanical concept enables precise mirror movement without additional bearings in the optical path.
Fields of application
Calibration of FLIR, IR, and EO/IR gimbals, Target motion simulation for autonomous sensors and weapon systems, Mirror control tests with defined motion profiles, Hardware-in-the-loop verification of optical tracking units, Development of algorithms for multi-target tracking and sensor fusion
782464:002.26 | X | Rz | Ry | |
Travel | [mm] [°] | 500 | ±160 | ±6 |
Repeatability unidirectional | [mm] [°] | ± 0.5 | ± 0.017 | ± 0.008 |
Repeatability bidirectional | [mm] [°] | ± 1 | ± 0.045 | ± 0.015 |
Positioning speed | [mm/s] [°/s] | 500 | 30 | 15 |
Max. speed | [mm/s] [°/s] | 1500 | 50 | 25 |
Max. acceleration | [m/s2] [°/s2] | 23 | 380 | 340 |
Max. load Fx | [N] | 50 | ||
Motor | AC Servo | DC Motor | DC Motor | |
Drive | Direct, Gear Box, Synchron Belt, Flexure | |||
Bearing | Profile Rail, Thin Section Bearing, Ball Bearing | |||
Feedback | Linear Scale, Motor Encoder, Motor Encoder | |||
Material | Anodized Aluminum, matte, black | |||
Optional Features | Housing, indeviduell targets passiv or active, larger area of motion, custom controls. | |||
Variants Cleanroom | up to clean room class ISO 6 (higher on request) | |||
Variants Radiation | - | |||
Variants Magnetism | - | |||
Variants Vacuum | on request |
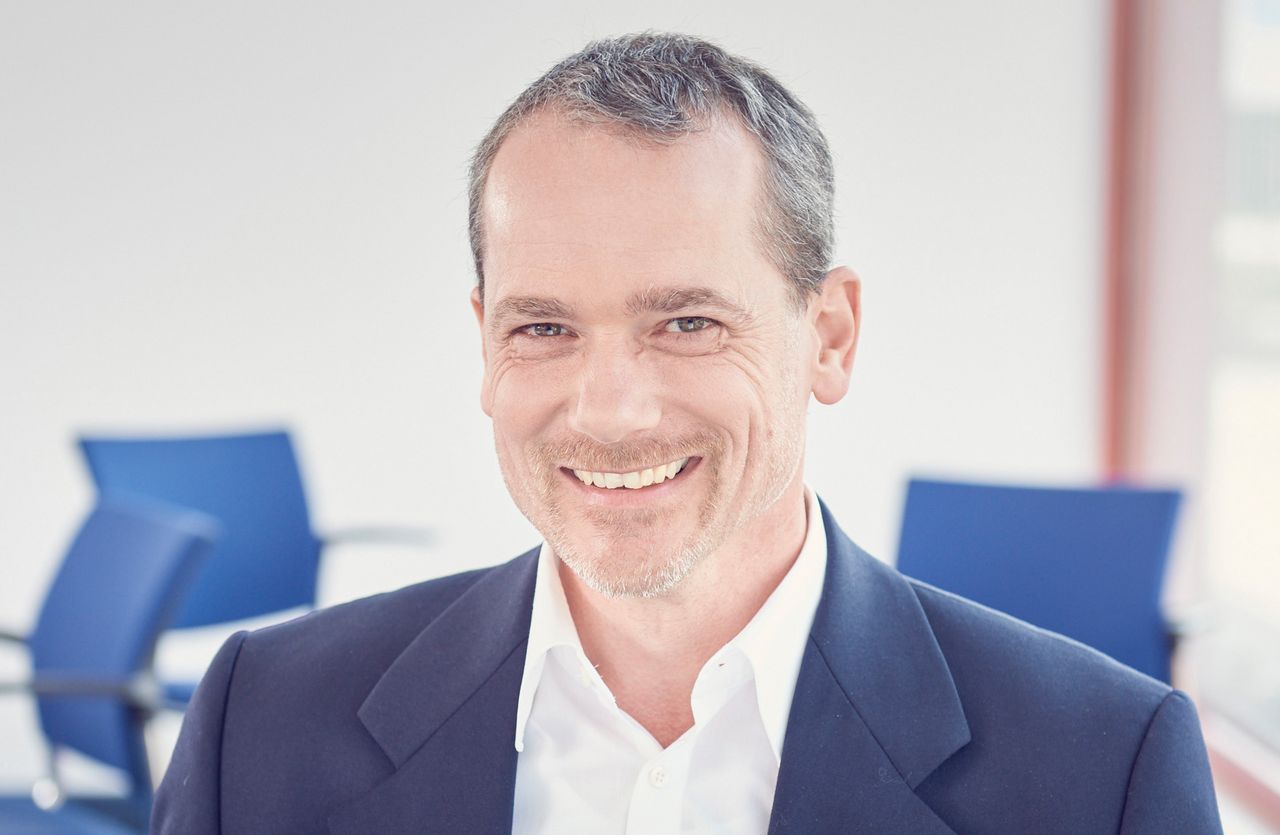
Elger Matthes
Consulting, Concepts, Innovation & Engineering
T +49 351 88585-82
E-Mail