Target simulator XZ | Calibration and training platform for EO/IR sensors & tracking
Precision Assemblies and Components
782464:001.26
The Target Simulator 3(XZ) is a high-dynamic motion system for realistic simulation of optical targets—such as light sources or visual markers—for testing, calibration, and development of modern tracking systems. Three target markers can be moved independently in two axes (X and Z), allowing them to appear closely stacked with minimal depth offset in the sensor’s field of view. The system is ideally suited for the development and qualification of EO/IR cameras, FLIR systems, MWS components, etc.
|
|
|
|
Options:
|
Reliable and process-optimised design
The mechanical design is based on a looped cable drive that enables motion along both the X and Z axes. This allows all actuators to be positioned outside the sensor’s line of sight. Motion is driven by precise DC motors with gearboxes, working together with profile rail guides to ensure smooth operation. The system achieves a repeatability of ±100 µm and supports speeds up to 510 mm/s with a travel range of 200 mm per axis.
Fields of application
The Target Simulator is used in a range of environments where EO/IR-based target tracking systems are developed, tested, or calibrated. These include FLIR and infrared camera systems, missile warning systems (MWS), and autonomous reconnaissance drones with optical target recognition. The system also plays a role in hardware-in-the-loop test environments and the training of AI-based tracking algorithms. It supports the development of real-time target detection and multi-object tracking.
782464:001.26 | X | Z | |
Travel | [mm] | 200 | 200 |
Repeatability unidirectional | [µm] | ± 100 | ± 100 |
Repeatability bidirectional | [µm] | ± 150 | ± 150 |
Positioning speed | [mm/s] | 350 | 350 |
Max. speed | [mm/s] | 510 | 510 |
Max. acceleration | [m/s2] | 0.5 | 0.5 |
Max. load Fx | [N] | 0.5 | 0.5 |
Motor | DC | ||
Drive | Gear Box, Rope | ||
Bearing | Profile Rail | ||
Feedback | Motor Encoder | ||
Material | Anodized Aluminum, matte, black | ||
Optional features | Housing, individuell targets passiv or active, larger area of motion, custom motion control | ||
Variants cleanroom | up to clean room class ISO 6 (higher on request) | ||
Variants beam | - | ||
Variants Magnetism | - | ||
Variants vacuum | on request |
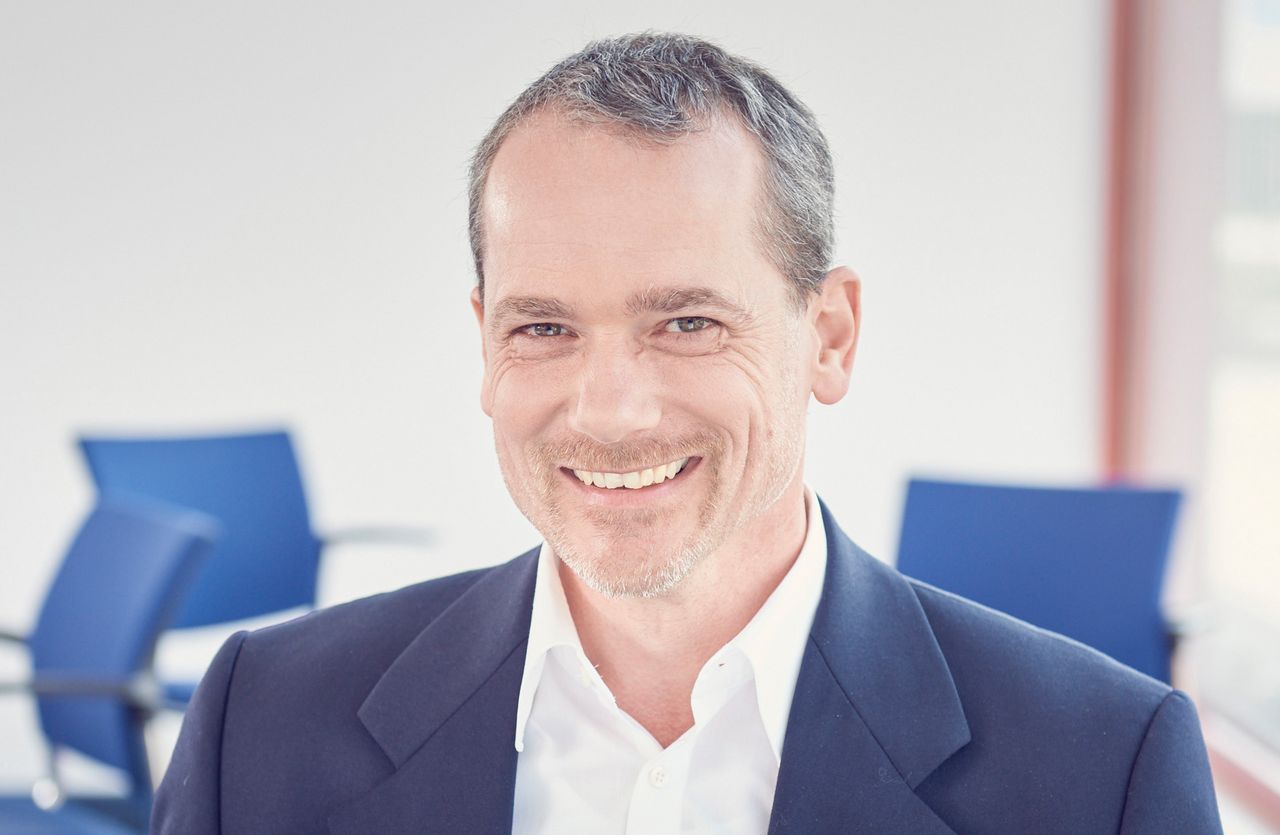
Elger Matthes
Consulting, Concepts, Innovation & Engineering
T +49 351 88585-82
E-Mail